오늘은 3D프린터에서 가장 일반적으로 사람들이 많이 사용하는 재료압출방식,
3D프린터의 기술방식과 기술단계에 대해 제가 시험 공부했을 때 요약했던 내용들을
올려볼까 합니다.
혹시 3D프린터 운용기능사 시험을 볼 예정이신 분들이 계신다면 유용한 자료가 되지
않을까 생각됩니다.
FDM/FFF 3D프린터
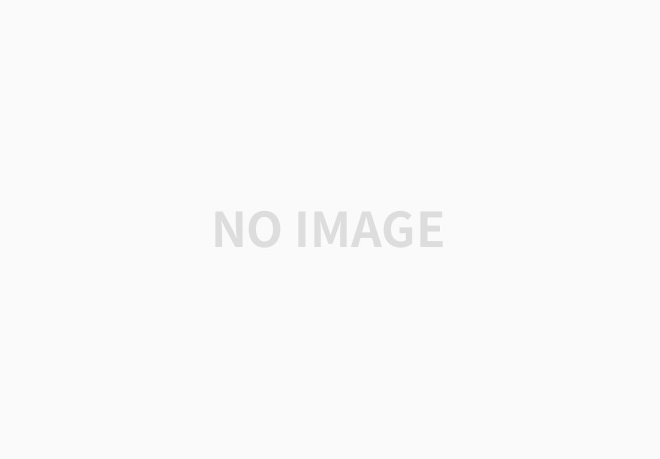
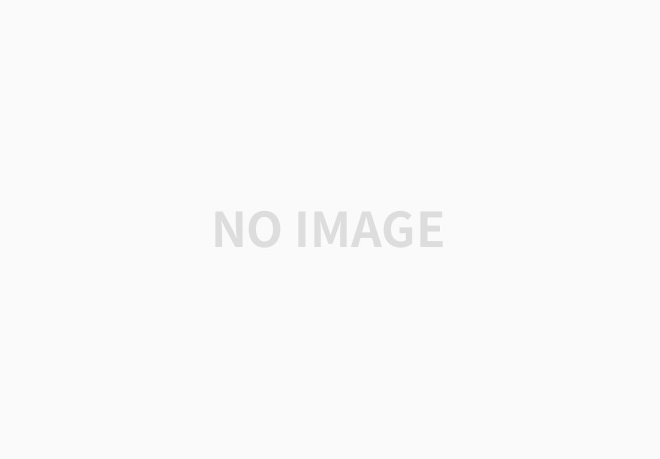
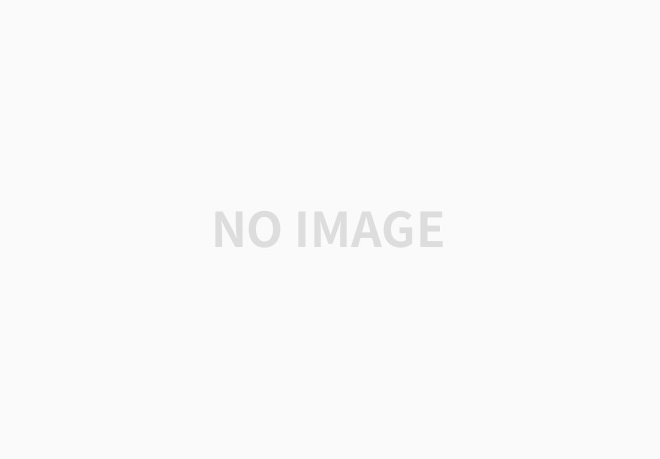
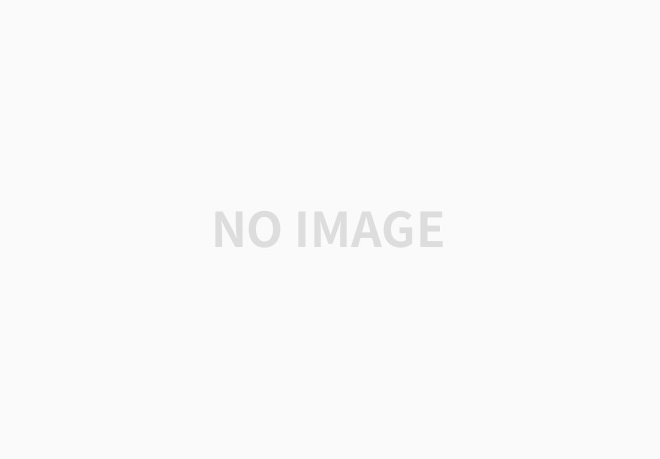
3D 프린터는 3차원의 물체를 제작하는 장치
(Apparatus for Production of Three-Dimensional Objects)
⇒ 출력 소재를 레이어(Layer, 층) 단위→ 적층 (積層, 층층이 쌓임)
→3차원의 물체를 제작
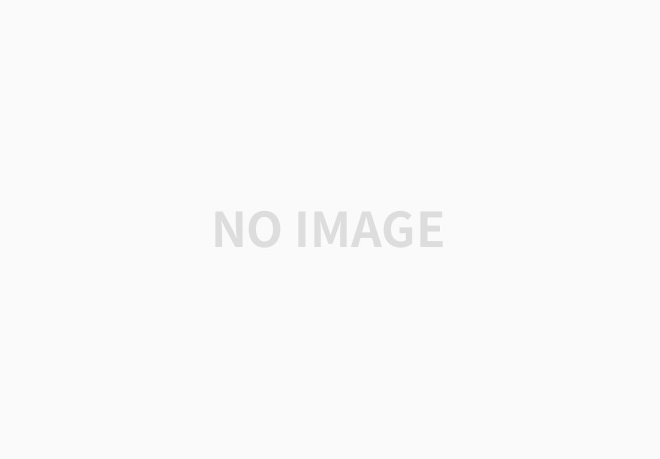
1) 3D프린터는?
☞ 3차원의 모델링 파일을 생성한 뒤 3D프린터로 출력하기 위한 변환작업,
사용되는 소프트웨어→ 슬라이싱 소프트웨어(CURA, 신도리코, FlashPrint etc...)
https://jhj60718442.tistory.com/20
3D 모델링 폴리곤, 패치, 넙스의 차이점
1. 모델링 ▶0차원(점), 1차원(선), 2차원(면)을 이용해 가상의 3차원(공간)에 물체를 표현하는 방식을 모델링이라고 한다. 가상의 3차원 면은 메쉬(Mesh), 생성된 오브젝트(object)는 지오메트리(Geometry
jhj60718442.tistory.com
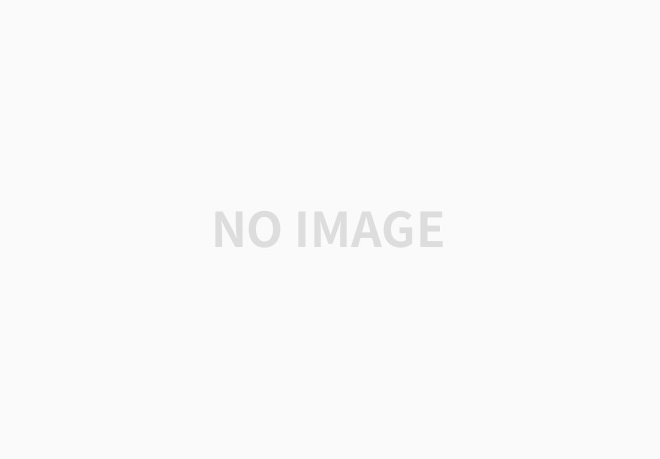
STL은 3D 시스템즈가 개발한 스테레오리소그래피 CAD 소프트웨어의 파일 포맷이다.
STL이라는 이름은 스테레오리소그래피에서 온 것으로
표면을 삼각형화시켜서 저장한다.
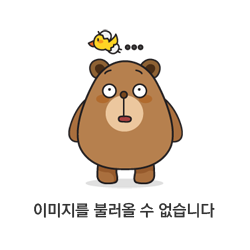
2021.08.02 - [왕초짜를 위한 3D프린팅 기초 실기 공부하기] - FDM 3D 프린터 방식
FDM 3D 프린터 방식
jhj60718442.tistory.com
2020.06.06 - [3D프린팅 첫걸음] - 3D 프린터 개념(2)
(2) 슬라이싱 소프트웨어
1) 3차원의 모델링 파일을 2차원의 X, Y, Z 좌표 값이 있는 레이어로 분해하여 재정렬
2) 3D 프린터 제어작업을 위한 G코드 명령어로 변환한다.
3) 출력명령이 실행되면 3D프린터는 첫번째 2차원 X,Y 좌표 값의 레이어부터 출력한다.
4) 레이어 두께만큼 이동하여 두번째 좌표 값의 레이어를 출력한다
----이렇게 반복 수행하여 마지막 레이어가 출력되면 3차원의 물체가 완성된다.
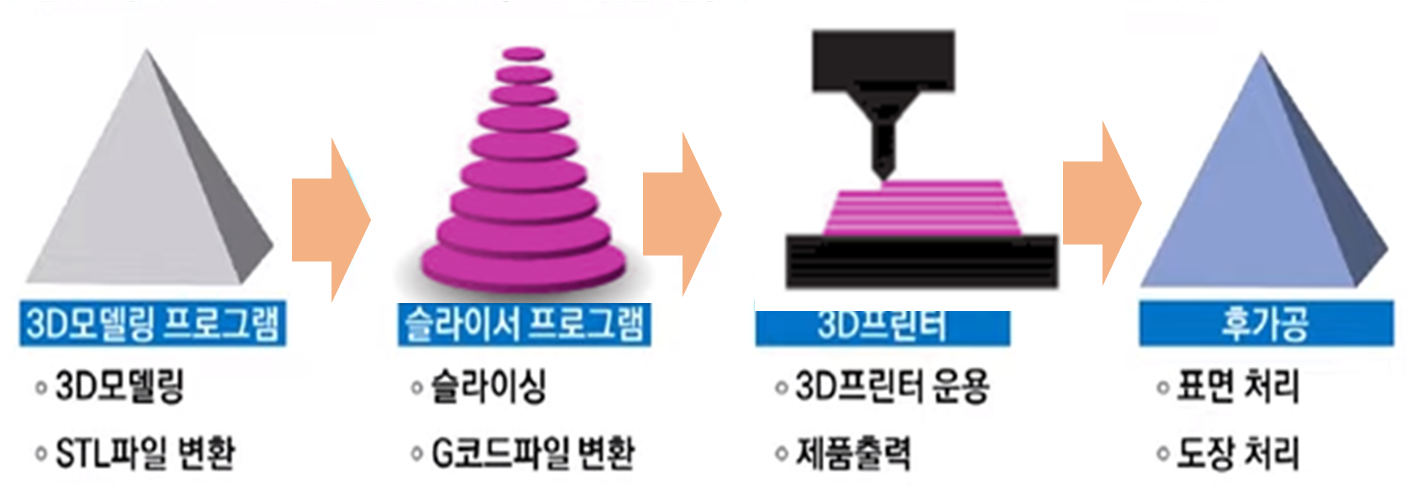
2. 3D Printing Process
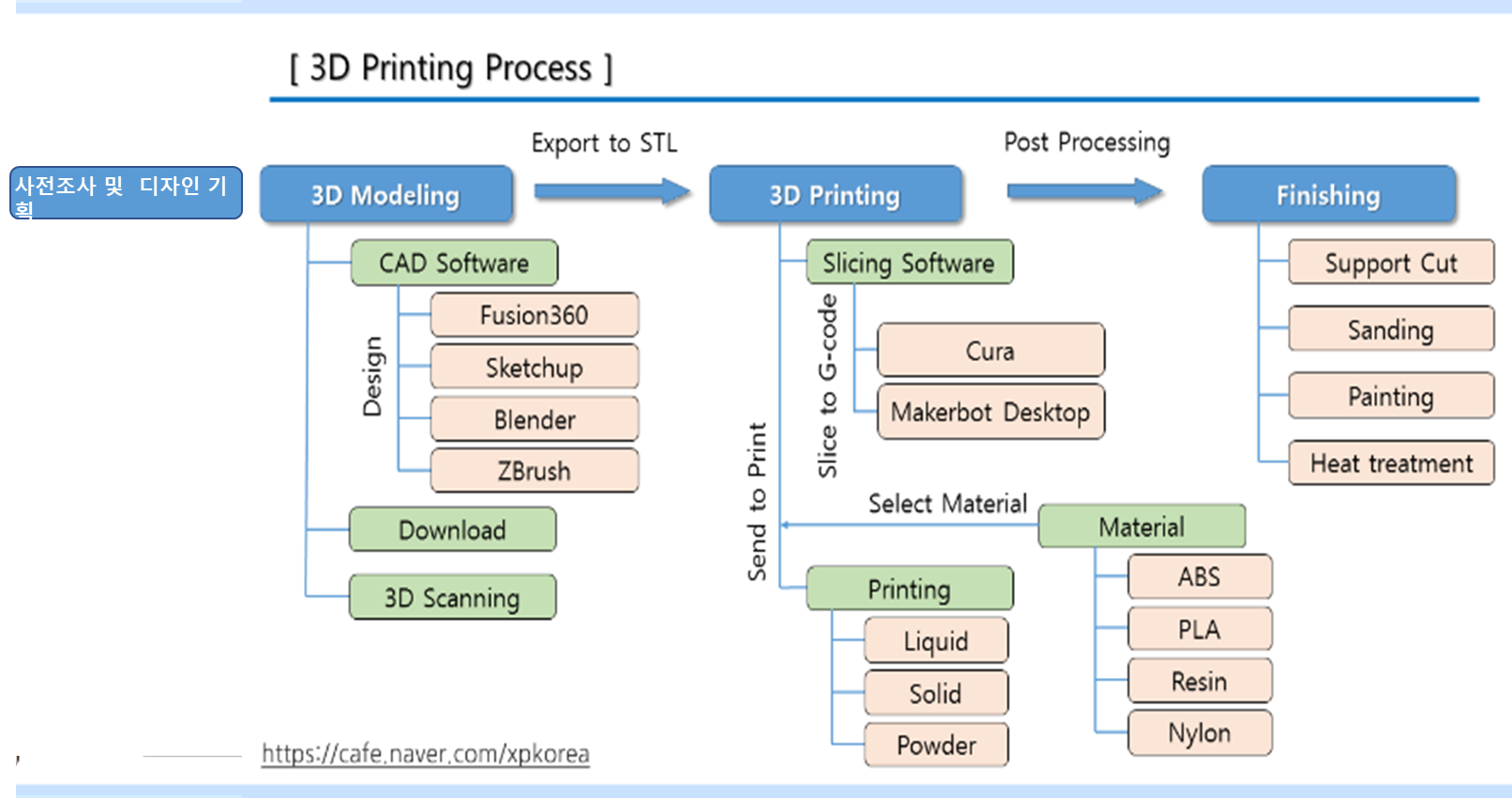

고체기반방식(SOLID) | 액체기반방식(LIQUID) | 분말기반방식(POWDER) |
∙ 고체재료인 필라멘트(Filament), 와이어(wire), 펠렛(Pellet), 시트(Sheet)등을 높은 온도로 용융시켜 압출, 접착제 이용, ∙ 시트나 필름을 접착 시킨 후 정밀 커팅을 통해 입체 물체를 제작하 는 기술이다. |
∙ 빛에 의해 단단하게 굳는 성질을 가진 광경화(photocure)성 액체 레진(liquid resin)을 사용. ∙ 이 소재는 레이저 빔, 강한 자외 선(UV)에 의해 경화되는 성질이 있다. ∙ 경화되는 성질을 이용해 액체 상 태의 폴리머 합성수지를 경화시 켜 3차원 물체를 제작하는 기술. |
∙ 분말(powder)상태의 재료인 석 고분말에 접착제를 분사하여 굳 힌다. ∙ 금속과 플라스틱, 모래 등의 분말 표면을 레이저 빔으로 소결. 3차원 물체를 제작하는 기술 |

ASTM에서 규정하는 대표적인 7가지 3D프린팅 기술방식은 제가 나름대로 정리해서
시험볼때 외우기 쉽고, 오래 기억하기위해 만든 표입니다.
공부하실때 도움이 되셨으면 좋겠네요~~
고체, 액체, 분말방식기반으로 컬러를 달리해서 컬러별로 기억하시면 기억이 오래 남더라구요
그래서 그대로 올려봅니다.
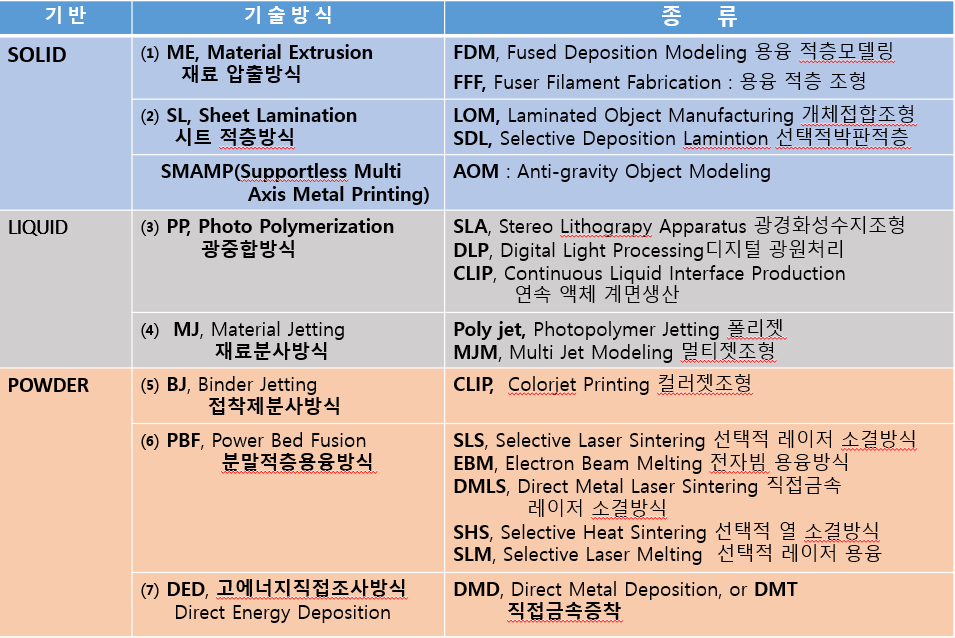

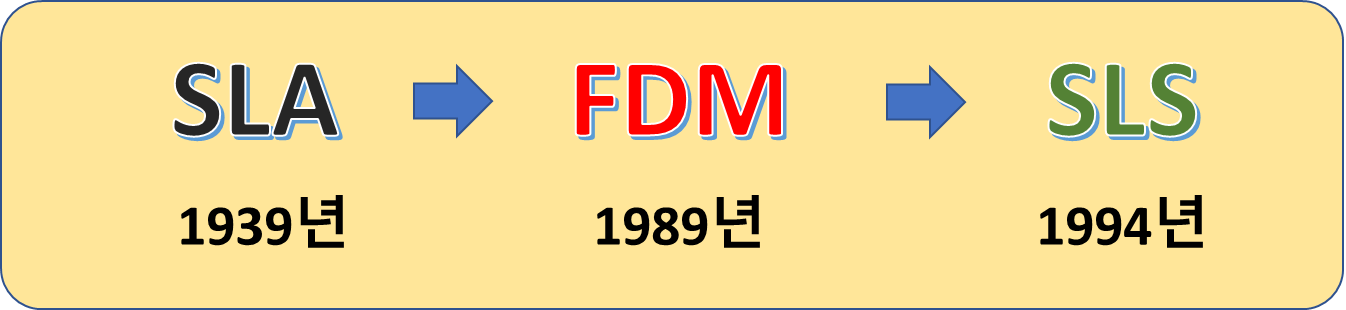

(3) 1939년 미국태생의 인물로 찰스 헐(Charles W.Hull, 또는 척헐(Chuck Jull))
'입체 인쇄방식으로 3차원 물체를 제작하는 장치'라는 이름으로 특허출원
☞ 이것은 세계최초의 3D프린팅 기술.
▶ 최초의 STL 포맷방식을 개발했다.
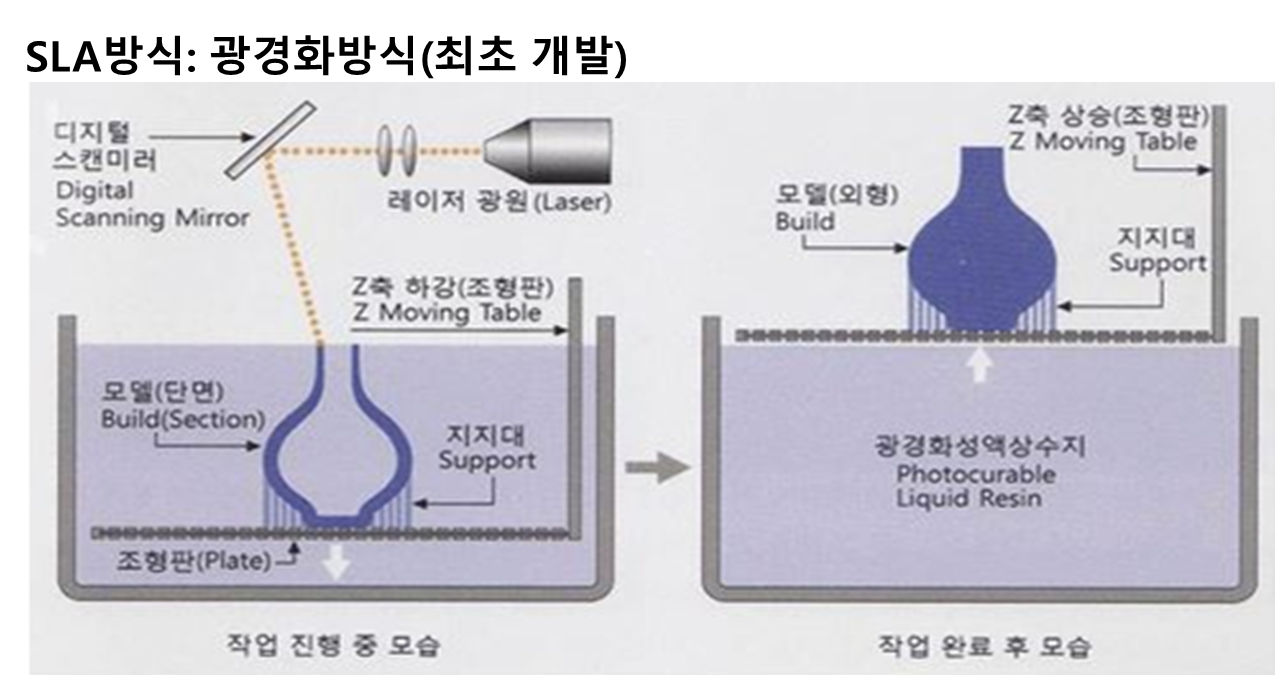
포토폴리머 (photopolymer) 광 경화방식
액체표면에 X, Y좌표 값 상의 정해진 위치에 자외선을 투사하여 하나의 얇은 경화층을 생성

1)1989년 “3차원 물체를 만들기 위한 장치 및 방법”
(Apparatus and Method for Creating Three-Dimensional Objects. 특허번호: US 5121329 A)‘,
용융 적층 모델링(Fused Deposition Modeling, FDM)방식 특허출원
▶ 항공 정비사, S. 스캇 크럼프(S. Scott Crump, USA)가 개발한 방식
리사 H. 크럼프(Lisa H. Crump)와 함께 스트라타시스(Stratasys)社를 설립.
⇒ FDM은 개인용 3D 프린터에서 가장 많이 사용되고 있는 방식.
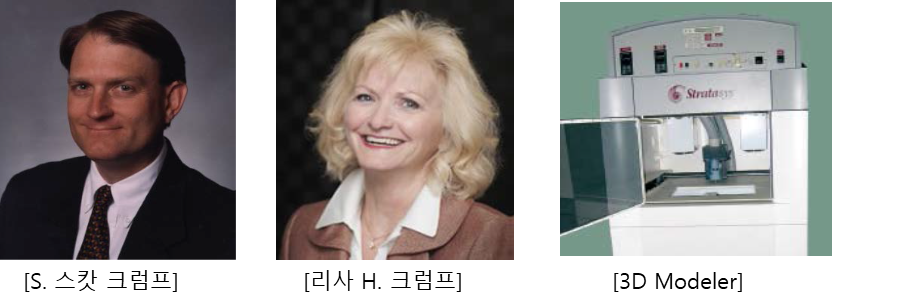
▶ Stratasys : - 메이커봇(Makerbot), 솔리드스케이프(Solidscape), 레드아이(RedEye) 등
- 디지털 제조 서비스를 별도 운영하는 자회사 소유
- 3D콘텐츠부터 시제품과 최종 제품까지 생산하고 있다.

"SLS 3D 프린터"는 선택적 레이저 소결(Selective Laser Sintering) 기술을 사용하는 3D 프린터입니다.
이 기술은 주로 나일론, 폴리카보네이트, 금속 등의 분말 소재를 사용하여 레이저로 층층이 소결(녹여서 굳히는)하여
3D 객체를 만들어냅니다.
▶1994년 ‘선택적 소결(燒結, 가루를 녹여 밀착시켜 굳힘) 방식에 의한 부품 생산 장치(Apparatus for producing parts by selective sintering. 특허번호: US 5597589 A)’라는 이름으로 특허 출원.
▶ 미국 텍사스 대학 오스틴(The University of Texas at Austin)
기계공학과(ME, Mechanical Engineering) 학부생 칼 데커드(Deckard, Carl), 조 비먼(Joseph
Beaman) 교수⇒미국 국방성(Department of Defense) 산하 기관인 국방고등연구기획청
(DARPA, 미국)의 후원,
▶ 선택적 레이저 소결 기술인 SLS(Selective Laser Sintering) 방식을 최초로 개발한다.

이 기술의 주요 개발자들에 대한 정보는 다음과 같습니다:
- Carl Deckard - SLS 기술의 발명자는 카를 데카드(Carl Deckard)입니다. 그는 1980년대 후반 텍사스 대학(University of Texas at Austin)에서 이 기술을 개발하였으며, 이후 이를 상업화할 수 있는 방법을 모색했습니다. 그의 연구는 1989년 특허로 이어졌습니다. 이 특허는 선택적 레이저 소결(Selective Laser Sintering) 기술을 최초로 공식화한 것입니다.
- Joachim L. Lutz - Carl Deckard와 함께 SLS 기술을 발전시키고 상업화를 위해 기여한 사람으로, 많은 기술적 조언과 연구를 했습니다. 그는 SLS의 초기 실용화를 위해 중요한 역할을 했습니다.
- 3D Systems - SLS 기술을 상업화하는 데 중요한 역할을 한 기업으로, 3D Systems는 1990년대 초반부터 이 기술을 상용화하고 다양한 산업 분야에서 사용되도록 도왔습니다.
SLS 기술은 특히 복잡한 형상의 부품을 생산할 수 있는 능력 때문에 자동차, 항공우주, 의료 분야 등에서 많이 활용되고 있습니다.
SLS(Selective Laser Sintering)는 고체 물질을 레이저로 가열하여 성형하는 3D 프린팅 기술 중 하나입니다. 이 기술은 주로 플라스틱, 금속, 세라믹 등 다양한 소재로 작업할 수 있습니다.
SLS 방식에서 가장 흔히 사용하는 재료는 나일론으로, 기계적 물성이 우수하여 인기 있는 엔지니어링 열가소성 플라스틱입니다.
나일론은 튼튼하면서도 가볍고 유연할 뿐만 아니라 충격, 화학물질, 열, 자외선, 물, 먼지의 영향에 안정적이기까지 합니다.
기타 인기 있는 SLS 3D 프린팅 소재에는나일론 복합재, 폴리프로필렌(PP), 플렉서블 TPU가 있습니다.
SLS(Selective Laser Sintering)는 고체 물질을 레이저로 가열하여 성형하는 3D 프린팅 기술 중 하나입니다.
이 기술은 주로 플라스틱, 금속, 세라믹 등 다양한 소재로 작업할 수 있습니다.
작동 원리:
- 소재 준비: 먼저, 분말 형태의 소재(예: 나일론, 금속 분말 등)가 프린터의 빌드 플랫폼에 균일하게 퍼집니다.
- 레이저 선택적 소결: 레이저가 이 분말을 표면에서 빠르게 가열하고 소결하여 단단하게 결합시킵니다. 레이저는 3D 모델의 외형을 따라 가면서 소결을 진행합니다.
- 층별 제작: 첫 번째 층이 소결되면, 그 위에 다시 분말을 얇게 추가하고, 다시 레이저로 다음 층을 소결하여 모델을 한 층씩 쌓아갑니다.
- 후처리: 출력이 끝난 후, 모델은 남은 미사용 분말에서 꺼내어 세척, 다듬기를 거칩니다.
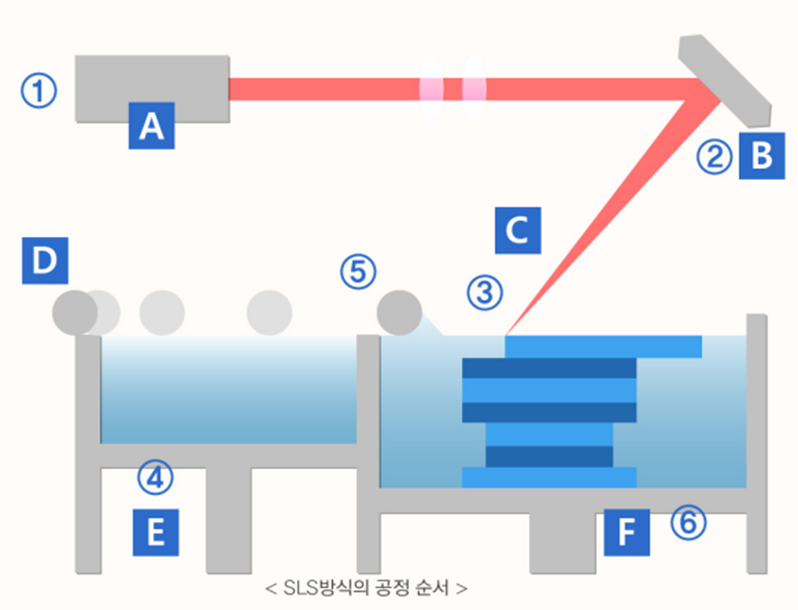
SLS 3D 프린터기의 장점
- 고해상도: 매우 정밀한 출력이 가능하여 복잡한 형상이나 세밀한 디테일을 구현할 수 있습니다.
- 다양한 재료 사용: 플라스틱, 금속, 세라믹 등 다양한 소재를 사용할 수 있어 다양한 산업 분야에서 활용 가능합니다.
- 후가공이 용이: 후처리가 비교적 간단하여, 예술적 또는 기능적인 후가공이 가능합니다.
- 기능성 부품 제작: 강도가 높고 내구성이 우수한 부품을 제작할 수 있어 기능성 테스트나 엔지니어링 부품에 적합합니다.
- 서포트 구조 필요 없음: SLS는 분말이 자체적으로 서포트 역할을 하므로, 추가적인 서포트 구조를 만들지 않아도 됩니다.
SLS 3D 프린터기의 단점
- 비용: 장비 및 소재가 고가로, 초기 투자비용이 높은 편입니다.
- 속도: 상대적으로 출력 시간이 길어 대량 생산에는 시간이 많이 소요될 수 있습니다.
- 후처리 필요: 출력물에서 남은 분말을 제거하는 후처리가 필요하며, 이를 위한 추가적인 시간이 소요될 수 있습니다.
- 소재 제한: 사용 가능한 분말 소재는 제한적이며, 새로운 소재 개발이나 연구가 필요합니다.
SLS 3D 프린터기의 활용도
- 산업용 부품 제작: 특히 항공우주, 자동차, 의료기기 등의 산업에서 기능적인 부품을 제작하는 데 많이 활용됩니다.
- 프로토타이핑: 제품의 초기 설계 단계에서 프로토타입을 제작하는 데 유용합니다.
- 맞춤형 제품: 개인화된 제품을 제작할 때 유용하며, 예를 들어 맞춤형 의족, 의치 등이 그 예입니다.
- 소형 대량 생산: 소량 다품종 생산에 적합하며, 맞춤형 부품을 여러 개 제작할 수 있습니다.
- 패션 및 예술 분야: 복잡한 디자인의 액세서리나 예술 작품을 제작할 때 사용됩니다.
결론
1994년 SLS 3D 프린터기는 기술 발전 초기였으나, 그 원리와 특성상 현재에도 많은 산업 분야에서 중요한 역할을 하고 있습니다. 특히 고정밀, 고강도 부품을 필요로 하는 산업에서 그 장점이 크게 부각되고 있습니다.